The Effect of the Epicflow methodology on a Project Department from a Metal Company
Arnold AG is a German specialist for high-quality products that are made of metal. Within the business units “Art” and “Project”, the company delivers high-quality sculptures for artists and sophisticated elements for superyacht manufacturers. Its customers are international well-known artists and design studios.
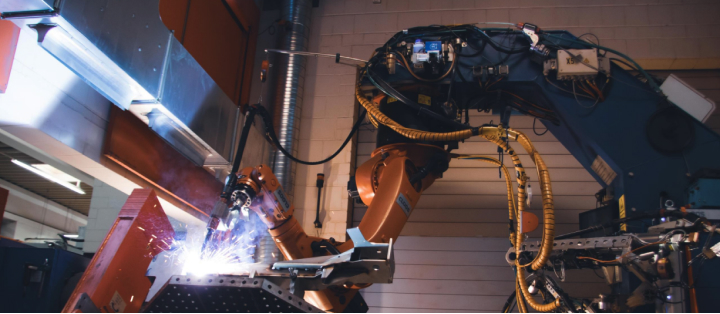
With Epicflow
Epicflow revealed opportunities to take extra projects in short notice which was not possible before.
As a result, Arnold AG got a true increase in throughput without extra labour costs.
The problem statement was
- Long uncertain lead times;
- Late delivery;
- Inability to set feasible due dates;
- Lack of understanding of the impact of taking extra projects;
- Inconsistency of planning approaches among project managers;
- Missing optimal 1:1 communication between project managers and production departments.
What we did
Just a few days of consultancy were enough to explain the concept of multi-project resource management used in Epicflow.
A few highlights of the training:
- Standard project template creation
We had a one-day workshop with all project and department managers to define a standard project template for all projects. - Estimation and capacity changes
We agreed to reduce all estimations by 25% in combination with a reduction of the available capacity per day also by 25%. By applying this method, we meant to eliminate student syndrome and gold plating effects. Now we had an ambitious estimation in combination with a capacity reserve and a 20% time buffer (float) till the end milestone. - Data setup
After the agreement, all project managers put their project data in the new template into the new system. - Projects overview
At the end of the day, we had a full overview of the whole portfolio including the load graphs based on the estimations. Possible bottlenecks were immediately visible and decisions were taken to resolve that
Results
In three months, the difference between the estimations and the reality became visible.
The schedules were adapted where needed.
Also, it became clear that the new data showed opportunities to take extra projects
on short notice. Management was not aware of this but then they understood that it was
possible, because the new system helped them to sell and deliver more with the same
number of people. They got a true increase of throughput without extra labour cost.
The standardization of the project plans resulted in the consistent approach to data interpretation. Everyone in the team had access to all the data that was the single
source of truth.
The involvement of C-level management was crucial. Mr. Ingo Stemmer (COO) contributed to the successful implementation of the system by supporting and motivating his people. He stayed throughout all the workshops exchanging ideas and feedback with the teams. It was an amazing collaboration!
The implementation was done by two German consultants from Alkyone Consulting GmbH and one Epicflow consultant.
TKF — A Dutch company providing building, industrial and telecom
solutions for the construction industry.
KPN — A Dutch landline and mobile telecom company
VieCuri — A Dutch top clinical teaching hospital.
An Aerospace and Defence company from the UK
A major pharmaceutical company