How TKF R&D Department Increased Output by 200%
TKF is a Dutch company with 85 years of experience producing building, industrial, and telecommunications solutions for the construction industry. What sets TKF apart is its continuous investment in the quality of service. This approach has helped TKF grow from a cable manufacturer to a leading supplier of connectivity solutions. Extending the company’s already broad portfolio of cables, systems, and services, TKF’s R&D department runs a complex multi-project environment in Haaksbergen, the Netherlands.
“Twelve years ago, TKF’s R&D Department found itself on the brink of multi-project chaos. With Epicflow they increased output by 200% and reduced lead time by 50% in 2 years”
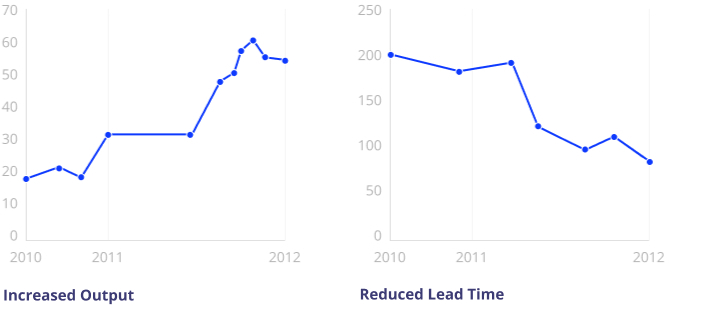
The Challenge
In 2005, TKF’s R&D Department found itself on the brink of multi-project chaos. It counted eighteen full-time engineers who had to manage 75 active projects. The number of existing projects was too high to determine the gating process for the new ones or even to make a close prediction. The team began to lose focus while the management was struggling with ineffective planning strategies and sub-optimal workloads.
Jan Willem Tromp, researcher & co-founder of Epicflow : “When I was invited to the R&D department of the cable manufacturing company the situation was as follows:
- There were 50 new product development projects and 22 engineers working on them;
- They had a list of activities/deliveries per project in Excel;
- Almost none of the projects was delivered on time and most projects had cost overruns;
- About 25 new products were delivered per year;
To remedy their weaknesses, the R&D department opted for MS Project, expecting this tool to help them with planning. In 2009, the company managed to complete 29 projects, but as could be expected, most of them failed to meet their due dates even though the number of engineers grew from 18 to 22.
Management was able to release projects only with solid business cases, and only 50% of the projects were released to market. They were executed in a structured way, but priorities still remained unclear. This was the turning point when managers realized that MS Project wasn’t enough to untangle their complex multi-project situations.
The Solution
To strengthen their approach, TKF’s R&D department started looking for a tool that could integrate with MS Project and upgrade it for a multi-team environment. As a result, they chose Epicflow.
Epicflow’s concept brought about a real change in the company’s climate. It promised to help TKF’s R&D department meet the above-mentioned objectives. The department saw visible changes, and Hans de Boer, the head of the department, reported back with the results he had been looking for. Project output doubled in 18 months, while the average lead time decreased by 50%. Team members were no longer overloaded, as project managers were able to balance workloads with actual capacity.
Results
Thanks to Epicflow, the R&D department managed to link all projects in one database and get a view of projects from the perspective of resources. One of the Epicflow’s features, the Pipeline, helped by showing updates on each project’s status and signaling in red when at least one of the engineers was overloaded. The system generated daily updated priorities for all tasks, and engineers could also know the urgency of each task in the pipeline. As requested, project managers got real-time insights into resource capacity and could control project statuses and carry out clear management reviews.
Within two weeks we found out that the 22 resources were heavily overloaded – their workload more than doubled their capacity. The R&D manager put 50% of the projects on hold to overcome the overload.
Positive results were increasing quickly:
The number of delivered projects increased from 25 to 48 in the first year, to 76 in the
second year and to 98 in the third year while the number of engineers went down to 17
(was 22).
Lead time was reduced to 3-4 months while previously it was 12-18.
Big projects were dropped into tasks which contributed to the increase in delivery by
200% in 3 years.
KPN — A Dutch landline and mobile telecom company
VieCuri — A Dutch top clinical teaching hospital.
Arnold AG — A German company creating high-quality metal products.
An Aerospace and Defence company from the UK
A major pharmaceutical company