Shipbuilding is regarded as one of the slowest, most complex, and most unwieldy industries. At the moment, there are approximately 2,500 shipyards and maritime companies around the world involved in construction, modification, maintenance, and repair of yachts, military vessels, cruise liners, and other cargo and oceangoing passenger ships. The maritime industry has remained stable for about fifty years and has continued to follow the shipbuilding traditions established in the previous century.
Chris Baraniuk, a BBC correspondent, reports that âmany vessels criss-crossing the worldâs oceans today are bulky, diesel-guzzling giants that havenât fundamentally changed in many years.â A few years ago, however, shipbuilding suffered a severe decline, leading top South Korean shipyards to multi-billion-dollar losses because preferences for mega projects have changed. The Paris Agreement brought with it new environmental regulations that have encouraged key shipbuilding industry players to start embracing automation and artificial intelligence to achieve climate goals. In this article, we explore fresh shipbuilding trends, define project problem areas, and suggest a way to balance project performance at shipyards.
New Trends in Shipbuilding
At the end of 2017, World Maritime News reported that the results of the annual Tripartite Shipbuilding Forum will force stakeholders to design new eco-friendly types of ships and embrace new technologies to achieve world climate goals and counter cybersecurity risks. Last yearâs themes, which extended to 2018, are decarbonization of ships, safe design, and digitalization.
The industry urgently needs new ship designs, equipment, propulsion systems and alternative fuels to achieve the CO2 reduction goals established by the Paris Agreement on climate change, and the specific objectives to be established for international shipping by the UN IMO as part of its GHG reduction strategy. â World Maritime News
Based on shipbuilding predictions by the International Maritime Organisation (IMO), the industry could become 75% more efficient in reducing CO2 emissions by installing LNG/LPG-fuelled engines and designing solar- and wind-powered ships. Even though industry representatives are somewhat pessimistic about integrating new changes to shipyards and are sure that the status quo will prevail, changes can already be noticed all over the world. Trying to bring shipping into the twenty-first century, Rolls-Royce has already taken the first steps to realize autonomous self-driving ships, RIMS has started to use drones to observe Korean ships, and the first robots have been deployed at shipyards. These projects couldnât happen without the ambitions of the people that stand behind them.
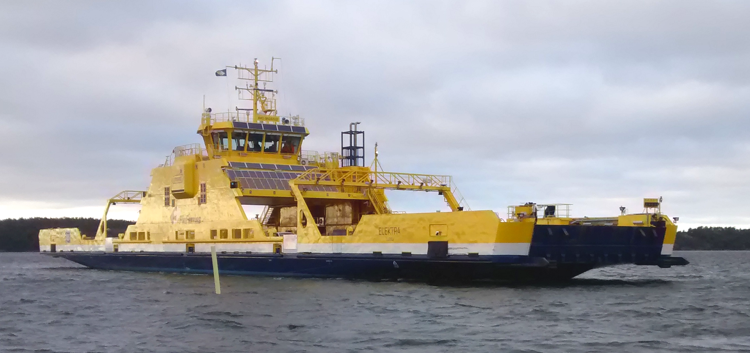
Scandinavia is bearing witness to a new generation of clean technologies. Credit: Alexander Love
Read more:Â How AI Will Change the Future of Project Management
Adapting to the trends of AI and digitalization in general, shipbuilding companies will contribute to creating more efficient and less harmful seaborne systems. Even minor repairs and fixes of vessels at the shipyard, however, will require careful attention by project managers, meticulous planning, and excellent vision. Thatâs why weâve collected opinions and lessons from industry leaders to keep you posted on the solutions that will set the stage for a new generation of ships.
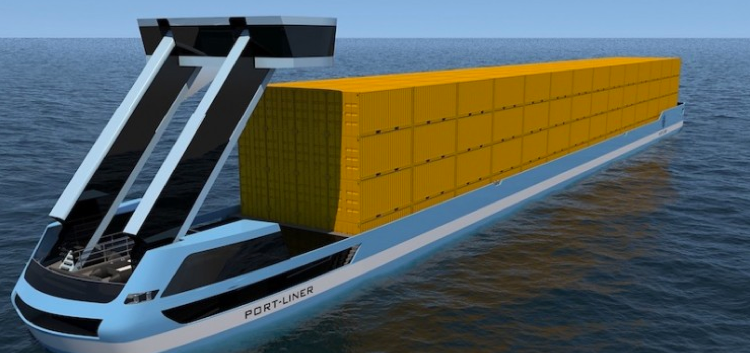
Dutch boat builder Port-Liner is launching a fleet of autonomous battery-powered barges in the Netherlands this summer. Credit: Omega architects
Problem Areas in Shipyard Projects
But first, letâs figure out what problems are on a shipyardâs radar as far as project management is concerned. Fernando Remolina, senior project manager at DAMEN Shiprepair Curacao and the author of Shipyard Project Management, the freshest book that sheds light on the role of a project manager in the shipbuilding industry, says that each project can cost between $500,000 and $10,000,000 in just ten days or two months. Remolina says that as a project manager youâll most likely have at least 500 activities to track and control on your scheduling software and will be able to repair from 15 to 25 ships per year. The scope is impressive, donât you agree? The ballast water treatment system alone, for instance, requires a year of project planning, while the installation procedure usually doesnât last more than 25 days.
Read more:Â 2018 Project Management Trends in Construction
According to Mohd Abdelmonem, assistant shipyard manager at NKOM, one of the main challenges as well for shipyards is to have experienced project managers who are able to manage these types of new trend projects, especially projects like LNG as Fuel conversions and Ballast water management system retrofits.
The challenges in these projects usually arise due to space constraint in the vessels and integration of the new system to the existing vessels’ system, which means that a minor engineering mistake might result in a major impact on the project cost and timeline. Another note, these projects usually have various stakeholders and many contractors and itâs challenging to align them towards one goal. The responsibilities have to be clearly defined between different parties and should not leave any gray areas, as eventually every party will be protecting its own interest. – Mohd Abdelmonem
Gustavo Pedreira, a marine project management expert at VARD and opinion maker, is convinced that risks in managing projects usually come from new designs (prototypes) that involve design drawings, calculations, and necessary equipment. He claims that prototypes always require more worker hours than vessels built before, costing more money and eating into profits, thus affecting the delivery time.Â
The LPG/LNG engine solution has been there for years. Whatâs missing is the shore gas terminal investment (making the gas available to refuel the ships). A few offshore supply ships have installed pure gas engines in Norway, where they get incentives and pay more taxes if they pollute more. Others have had a more pragmatic approach, installing dual-fuel engines, which are less efficient in performance and anti-pollution, but less dependent on LNG fuel stations. On top of that, battery and battery bank systems have been added too, reducing fuel consumption. All these changes affect design, quantity of man-hours estimated/used, and bring more risks for project managers to handle. –Â Gustavo Pedreira
When managing shipyards, Pedreira has also noticed the following obstacles:
- Not all owners and superintendents have a great spirit of cooperation with a shipyardâs PM. Inspectors love to change things, not approved easily, and complain more on the âyard standard.â
- Trust between the ownersâ representative and shipyard workers takes time to build.
- Not all vessel types and sizes are meant to be built in all shipyards.
- A shipyardâs resources are not unlimited, so PMs for different projects fight internally for painters, scaffolding, internal logistics, etc.
Jan Mark Molenaar, project manager at De Keizer Marine Engineering BV, who is responsible for delivering maritime electrical installations, revealed to us that electrical installation projects in superyacht building are very complex in the sense that PMs have to face a lot of repetitive actions on different systems with small adjustments, each estimated in ranges of 100,000 hours. Itâs very important to get early warnings to increase capacity and to set the right priorities.
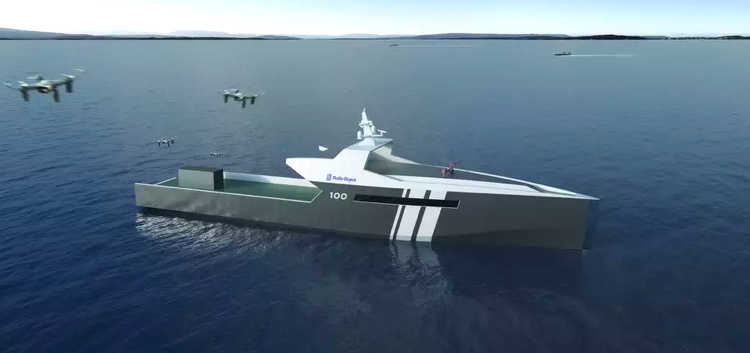
Autonomous ship concept. Credit: Rolls-Royce
What Tool Adapts to Your Project Environment?
Based on his considerable experience as a shipyard project manager, Remolina argues that the first step to on-time and on-budget project delivery is to âunderstand the effort spent during project duration and know the number of man-hours spent on a similar project.â Project management software exists that will let you balance actual capacity and workloads and find the optimal speed for your teams â the Epicflow add-on to MS Project and Jira. This software tool will ensure that you can better understand what the bottlenecks are that hinder overall progress. Epicflow helps project managers spot the weak places across shipyard projects, as it functions at the resource level. Youâll be in control of the sustained implementation of digital technologies and see the effects on your employees. With Epicflow, youâll get access to analytics:
- Pipeline with multiple projects will show your bottlenecks, so you can immediately release them.
- Historical load graph that presents group performance, capacity, load, and output over time
- Future load graphs for helping them take control of resource planning and predicting the impact of additional projects on the existing projects in the pipeline
- Prioritized task list guides your team to work faster and smarter across multiple projects.
- User mapping, showing the progress of the resource pool and balancing resources across groups
We believe that the automation of planning and prioritization, as well as a better perspective on all your projects, is key to managing flow at a shipyard. Schedule a free live demonstration of Epicflow with our researchers to discuss your specific case and problems in shipbuilding environments.